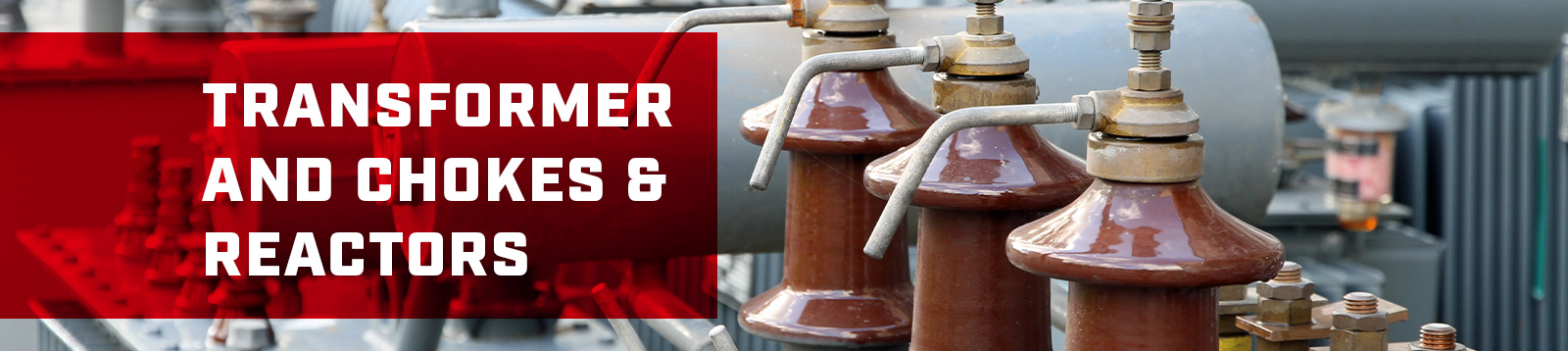
Request a FREE consultation.
Register NowA transformer is an important part of every power transmission system. Any failure in these can lead to power outages and costly and repairs. Here are some challenge areas that need to be addressed to be able to manufacture reliable transformers.
Inner Oil Tank
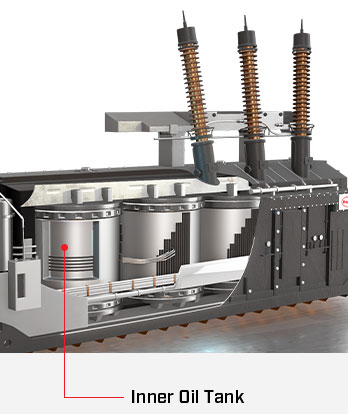
Challenge 1: Oil leak from threaded assemblies
Transformers are susceptible to oil leakage due to the vibrational loosening of threaded assemblies, which can further lead to breakdown of fins, flanges, valves and seals.
Solution: Lock assemblies and lid screws with LOCTITE 243 Threadlocker
Challenge 2: Leakage and peeling off paints
Electrical transformers are designed for 50-year lifecycles. But not their paint jobs. When exposed to air before welding without anti corrosion treatment, the paint peels off and leads to rusting and oil leakage.
Solution: Apply LOCTITE Color Guard Primer to protect your transformers from
Oil Tank Lid
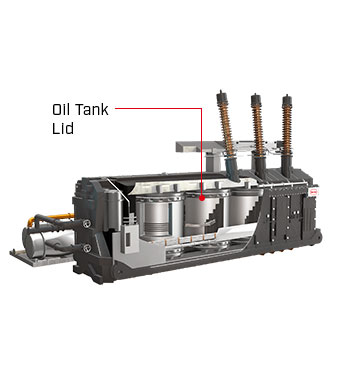
Challenge 1: Cooling oil loss from flanges
Due to continuous vibration, the screws of transformer flanges loosen up and leads to cooling oil loss, which increases oil usage, damages the transformer and interrupts power supply.
Solution: Seal flanges with 5900 Gasketing Compound
Name Plate
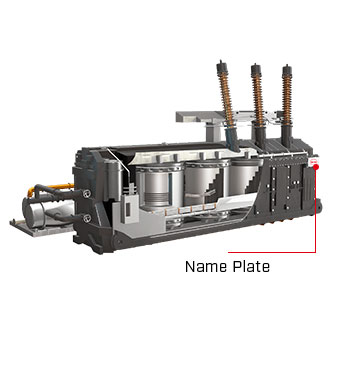
Challenge 1: Vibrational loosening
Under continuous vibration resulting from regular operations, the rivets or bolts of name plates loosen up and eventually it leads to the name plate falling from its place.
Solution: For higher strength, fix the name plate with LOCTITE HY 4090
Ferrite Cores
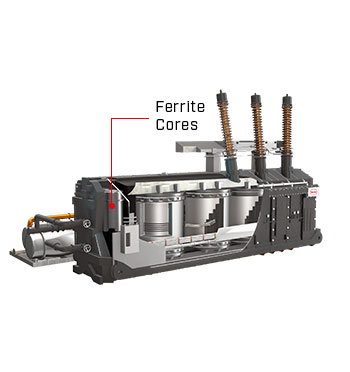
Challenge 1: Breakage of bonds between the cores during shipment
Damage during shipment weakens the bonds between cores resulting in lower strength and more chances of winding failures.
Solution: LOCTITE 5910 provides the strength and shock resistance for coils to withstand the winding process
Large Threaded Valves
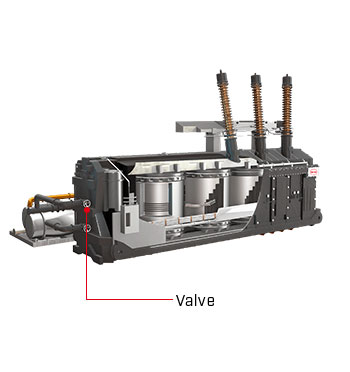
Challenge 1: Oil Leaks
Normal sealants applied on coarse threads, can't withstand the exposure to high temperature oil and lead to costly oil leaks in large threaded valves.
Solution: LOCTITE 5770 fills all voids between large, coarse threaded fittings, while maintaining a seal at up to 530 °F.
As a choke or reactor manufacturer you face demanding market requirements for increased product durability, greater electrical efficiency, reliability and lower production costs. We offer reliable and cost-effective solutions to help manufacturers to improve performance and reduce overall costs.
Lamination bonding
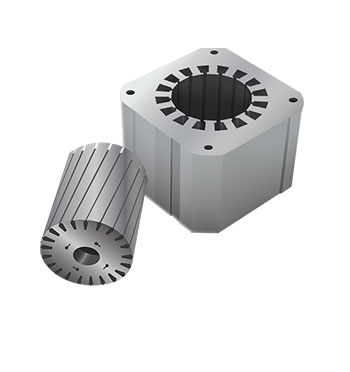
Challenge 1: High temperature resitance
Temperatures can soar up during regular operations of chokes and reactors. This requires a lamination bonding method with high temperature resistance, with most regular adhesives only being able to provide resistance upto a 120 degrees celsius
Solution: Bond with LOCTITE EA E-30HV and get temperature resistance upto a 180 degrees celsius
Challenge 2: Maintaining proper clamp load
Bolts can work themselves loose because they are always under strain caused by torque. Also, vibration, thermal expansion and contraction, and shock all contribute to loosening and reduction of clamp load.
Solution: Lock nuts and bolts reliably with LOCTITE 243
BEST SELLER PRODUCTS
- LOCTITE 8201 LubricantRating:80%
- Loctite 243Rating:100%
Locks and seals metal nuts and bolts to prevent loosening due to shock and vibration. Medium strength, removable with hand tools.
Learn More - Loctite 406Rating:100%
Loctite 406, low viscosity instant adhesive for bonding plastics and rubber materials
Learn More - Loctite 401
Loctite 401, general purpose instant adhesive for use on porous substrates
Learn More - Loctite 415Rating:100%
Loctite 415, high-viscosity instant adhesive for bonding metals, rubbers and plastics
Learn More - Loctite 495
Loctite 495, general purpose, low viscosity instant adhesive
Learn More - LOCTITE SF 7649
Loctite SF 7471, Activator for increasing the cure speed of Loctite anaerobic products
Learn More
Get a deeper understanding about minimizing downtime and increasing productivity in a plant
-
Reliable bonding solutions for electrical component manufacturers
Slow curing of epoxy results in production backlog and leads to increase in manufacturing and shipping cost. See how a choke and reactor manufacturer in the same situation found a way to avert such extra costs.
Know more -
Effective alternative for welding transformer
For transformers, welding of oil tank mostly leads to leakage and higher maintenance cost. See how LOCTITE helped a transformer manufacturer to achieve effective results.
Know more
Sorry, this can not be processed now.